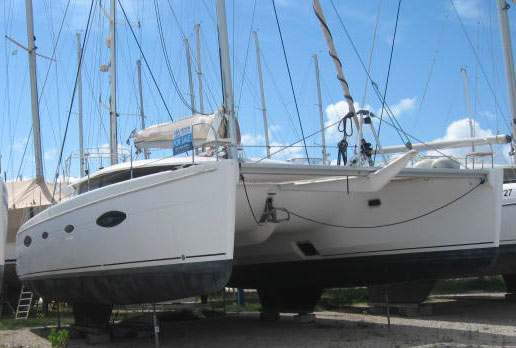
2. Keel.
2.1
The vessel’s hulls have fin/skeg long keels and they are separate pieces to the hull mould. The fins are bonded into a socket in the hull and are low enough to give protection to the sail drives. This means that the vessel can dry out at low water in tidal areas.
2.2
The keels were sighted from different positions and looked to be at a fair angle to the hulls.
2.3
Overall, the keels surfaces were found smooth with only a few small areas of damage. The keels were supported on two wooden beams which ran almost the full length of the keels. This prevented access for inspection of the bottom of the keels.
2.4
The port hull at the forward end of the skeg had a small area of damage. The wooden support beam made access difficult to see the full extent of the damage. This beam will need moving aft slightly to enable this area of damage to be repaired. It will need grinding back to good laminate and re-laminating with epoxy resin which has a superior bonding strength.
Recommendation: The wooden block supporting the keel will need moving aft to allow access to the damaged area. The area will need grinding back to good laminate and then re-laminating using epoxy resin. (A)
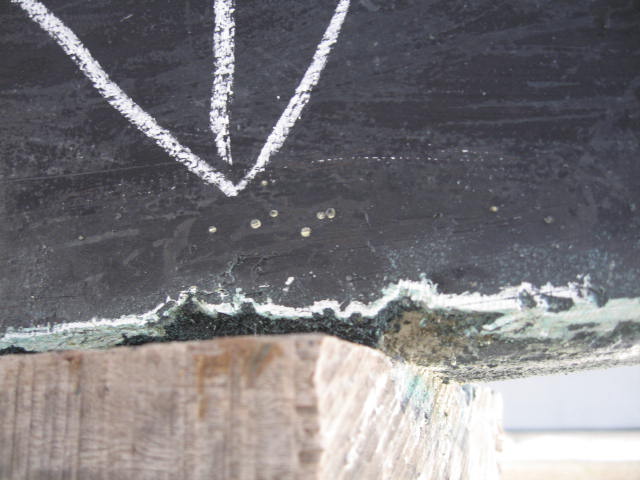
11. Stern Gear.
11.1
Two Volvo saildrive systems with three blade folding propellers.
11.2
The 18 x 16 (18 = diameter 16 = pitch) LH propellers with high skew blade tips. A part number was on the boss which was 3584032. The propellers are in good order with no damage or corrosion noted. These were heave tested and no play was noted in the folding mechanism.
11.3
The saildrive legs are in a satisfactory condition with no damage or corrosion. Weight testing confirmed that the legs were secure with no undue movement.
Note: Volvo recommend replacing the saildrive diaphragm seal every seven years. Inquiries should be made to see if the seals have recently been replaced.
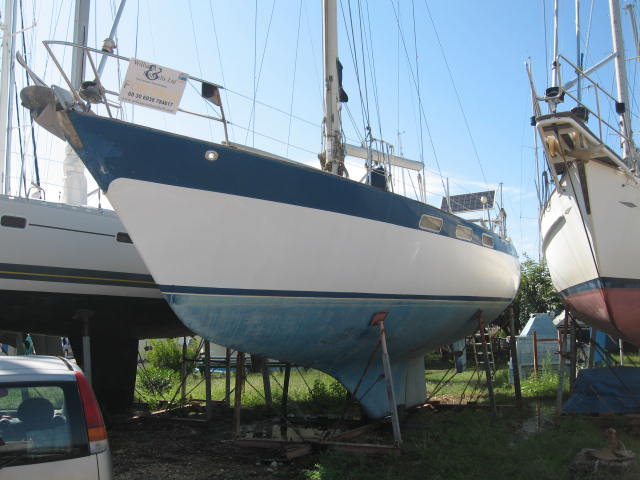
5. Deck moulding.
5.1
The GRP deck was moulded using chopped strand mat, woven rovings and white pigmented gelcoat externally. Flat areas of the deck are of sandwich construction with end grain balsa core stiffening. Plywood is usually incorporated into the laminate in way of load bearing fittings and areas of high stress.
5.2
The deck was integral with the Coachroof and Cockpit, no stress crazing was noted around rigging attachment points or load bearing fittings.
5.3
The mast is deck stepped, a load bearing, polished stainless-steel pole is positioned beneath the mast in the main saloon. There was no signs of cracking or damage and no distortion noted in the deck around the mast step.
5.4
The deck had a teak overlay which is badly worn. In certain areas, mainly starboard side forward, the deck had become detached from the deck laminate. In several areas the paying is worn or missing. When originally laid the teak was bonded and screwed to the deck laminate. This can be seen because lots of the wooden screw plugs are missing. When screws are driven through the top of the solid laminate this provides a potential path for moisture to enter the balsa core. Moisture readings cannot be taken on the teak itself and inside the vessel few areas exist where the deck-head can be accessed. Therefore, I cannot say for sure that no underlying problems with the balsa core are present, without destructive testing. Moisture readings were taken around deck fittings where possible and found to be low.
5.5
A small hatch had been retrofitted in the deck on the starboard side forward. The section of deck which was cut out to fit this hatch was found in one of the cabins. I was able to see from this section the thickness of the teak decking and the condition of the balsa core which was good. Unfortunately, this does not mean that the rest of the deck is in the same condition.
5.6
The deck was heavily walked on and found firm underfoot except for one small area. Just aft of the port side mast pulpit, is a small area where the deck is not firm. Pressing down with one foot, I found some flex to the deck, which is not the same on the opposite side. From the section of the deck that I found, altogether the deck is 40 mm thick. The balsa core is 20 mm, the top and bottom laminate is 5 mm each and the teak deck was 10 mm.
Recommendation: The areas where the teak had become detached from the laminate will need lifting and re-bonding to the laminate. All missing paying and missing screw plugs will need replacing. (A)
9. Bulkheads and structural stiffening including internal mouldings.
9.1
Several components contribute to the overall structure of the vessel. A, the internal bulkheads, B, longitudinal stringers and C, furniture and mouldings which have been bonded in.
9.2
Where seen due to restricted access, beneath inspection panels, in the engine compartment, under the bunks and in any other compartments. All the reinforcements appear to be firmly fibre glassed in with no signs of cracking or movement.
9.3
However, a problem exists with the bonding of the transverse bulkhead on the starboard side between the saloon and forward head. In the bilge area the plywood on this bulkhead had rotted and the laminate had parted from the plywood. The cause of this is a leak from the shower tray in the head, which had not been made watertight when fibre glassed in.
9.4
A problem exists with the bonding of the longitudinal bulkhead of the aft head. The shower tray of the aft head had also been leaking and this had caused the plywood around the shower tray to rot. The same recommendation is given for the repair of the forward head. Figure 11
Recommendation: The rotten plywood must be replaced, and the bulkheads must be re-bonded to the hull. The shower trays will need re-fibre glassing to make them watertight.(A)
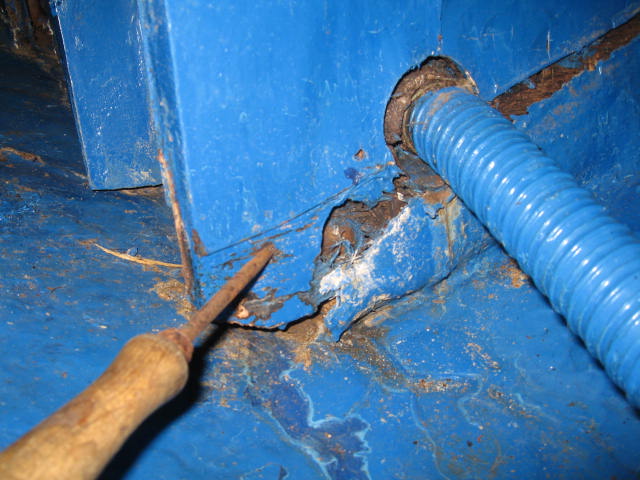
32. Gas Installation.
The UK Maritime Coastguard Agency (MCA) has a Code of Practice for commercial vessels, requiring specific gas system standards. LPG on board vessels can be dangerous if safety precautions are not followed. Insurance companies are asking that vessels conform to the current safety standards. Therefore, ALL gas systems are subject to the checks listed below as part of this survey.
a) Condition and efficiency of self-draining bottle storage.
b) Age and condition of flexible hose, is it supported and not under stress?
c) Age and condition of the regulator.
d) Condition of the copper tubing where accessible.
e) Are all appliances fitted with flame failure devices on all burners?
f) Is each appliance fitted with an isolating valve?
g) Is a gas alarm fitted.
a) Two 2.75kg gas bottles were secured in a dedicated gas-tight locker in the cockpit on the port/starboard side that drains directly overboard through drains to the atmosphere.
b) ISO 2928:2021 is the current specification for (LPG) rubber hoses, with working pressures up to a maximum of 25 bar. Gas hoses must be changed every five years; 2012 was seen on the gas hose, so, out-of-date.
c) The gas regulator had no date but looked old and corroded; if you don’t know the date, it is best to be safe and change the regulator; they don’t cost much money.
d) The pipework was solid copper from the locker to a stop cock at the cooker. There was no access to the copper pipe between the locker and the galley.
e) The two burner hob, an integrated grill, and an oven with flame failure devices.
f) A gas stop cock was seen in the galley and functioned open and closed.
g) No gas alarm was installed onboard.
33.3
Water maker fitted but not used or serviced for some years (brokers details)
Note: If Water makers are not treated with a storage biocide when not in use for long periods. Nasty stuff can grow on the membrane causing damage and an expensive replacement.
Leave a Reply